Continually pushing the boundaries of lifting
Both Huisman and Heerema Marine Contractors have a passion to push the boundaries of what is possible today. For more than a decade, Huisman has supported Heerema with its ambitions to be at the forefront of the industry – to be able to lift higher, heavier loads, with maximum outreach.
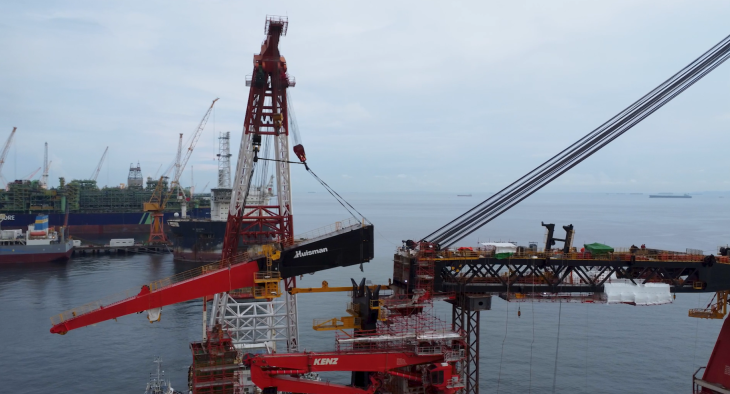
With almost 60 years of experience in the offshore energy industries, the Heerema Group assists in the design, construction, transport, installation and dismantling of offshore installations.
Huisman has carried out several projects for Heerema over the years, but this article focuses on the latest upgrade performed on the ‘Aegir’, one of the largest monohull crane vessels in the world. The lifting capacity of the second main hoist was increased from 2,000mt to 3,200mt, at a height of 110m, making the vessel ideal for the installation of large jacket foundations.
Koen de Vette, Proposal Lead Services Huisman, comments: “We were very pleased to collaborate with Heerema again on this important upgrade for the Aegir. We started with a FEED study and immediately set about examining how we could optimise capacity and planning, allowing Heerema to also give a clear answer to their end-client at an early stage.”
Larger and heavier wind farm components
The decision to carry out this upgrade was prompted by developments in the offshore wind sector and shifting client requirements. Higher lifting heights are needed to handle larger and heavier foundations and components. Coen Reissenweber, Manager Sales Service, says: “We are here to support clients who have an increasing focus on enhancing their equipment and to make sure that they can improve their workability. Aegir was originally designed as a pipelaying vessel – perhaps performing a few lifts a week – but now changes in workability are required because the offshore wind market involves projects with much more repetition.”
Edwin Kuijt, Heerema Marine Contractors' Project Manager - Business Unit Wind, explains that Heerema was looking to gain some additional flexibility from its second main hoist. “We are often working at huge heights and to the limits of our capabilities, but we know Huisman can support us and push further.”
Coupled with the development in the renewables sector, Heerema’s end-client Ørsted, required more capacity for the Greater Changhua offshore wind farm project in Taiwan, which is due to be constructed in 2025. At Greater Changhua the crane vessel will be installing 66 heavy suction bucket jackets of around 2,400mt.
“Heerema and Huisman have worked very closely together for many years, and this includes during the tendering and detailed design phases. As we have this long history together, we could already team up again when Ørsted contacted us at a very early stage,” Edwin adds.
Choice of manufacturing and ICT locations
The two companies worked closely together to decide the most suitable location for manufacturing the crane section and where the Installation, Commissioning and Testing should take place. Huisman fabricated the new boom section, weighing 160mt, at its own facility in China. This is the Group’s largest production facility, representing a total yard area of 284,000m2. Heerema then picked the section up in China and shipped it to Singapore for installation.
Edwin explains: “We chose Singapore for the ICT location based on the vessels’ operating area at that time. Additionally, Heerema has a lot of experience in Singapore. It is where we built the SSCV Sleipnir, our renowned semi-submersible crane vessel.”
Rommert Dijk, Huisman Project Manager of the Aegir, points out that the upgrade was quite a logistical challenge. The new lower block and block basket were manufactured at Huisman’s facility near Rotterdam and shipped to Singapore. The huge 3,200mt hook was cast in Austria and this together with other parts was transported from the Huisman HQ in Schiedam to Singapore by Heerema.
Meticulous preparations
Really tight planning was in place for the ICT period of just 94 days. All the components had to be in Singapore, as well as a large team of Huisman Engineers. Huisman formed a multidisciplinary team from various locations.
Koen de Vette adds: “The level of detail in the planning is astonishing. For example, assembling the team we had to fully schedule the tasks each day during the ICT period. And all these people coming in from various locations worldwide all had to have the right paperwork, visas etc. Every scaffold and every lift are carefully planned. This is only possible because we have a very experienced planning team and a good collaboration with Heerema in the preparation and execution phases.”
The timeline was also critical. Given that some items such as large bearings could have a lead-time of 36-40 weeks and the hook casting 40 weeks, it was vital to order crucial parts on time.
Risk management
Rommert adds that risk management was also extremely important. “At Huisman we know the enormous costs of having these vessels alongside the quay and they have limited availability.” One example of derisking the project was having the hook tested before it got to Singapore. Every hook is rigorously tested before it leaves Huisman’s HQ in the Netherlands at its own testing facility. And in Singapore, the required equipment for the load tests, arranged by a local subcontractor of Heerema, were available.
Given the complexity of the upgrade, there were several challenges to overcome – technical, a tight schedule, and logistics to name a few.
“The engineering was very challenging to make this upgrade happen. Huisman made all these complex calculations, and we closely monitored the progress in regular meetings. And now for sure: the hoist is really at its limits,” Edwin stresses. “By working in cooperation together, we jointly decided to reinforce the bottom chords on the main boom to maximise the lifting capacity at the desired radius. At a very early stage we decided to do the ICT with an additional temporary support on deck. This additional support worked out very well, also for the reinstallation. We could accomplish the project in a very short timeframe and successfully meet the schedule.”
Additional versatility
Edwin emphasises: “Definitely the Aegir’s new lifting height and capacity is valuable today and for new tenders. This additional versatility of the crane is really beneficial, especially for the offshore wind sector.
“For the future we are well positioned with our crane vessels and in line with market demands. This upgrade, together with SSCV Thialf and SSCV Sleipnir, means we’re ahead of the pack!”
Coen adds: “Huisman and Heerema are aligned, both family owned, with an innovative mindset, and both want to be the best in their industry. We want Heerema to be successful and through long-term partnerships we have supported them for over 25 years, and we will continue to do so in the future.
“I am most proud of the cooperation - from the first lead to the delivery of an upgraded crane. We delivered exactly what Heerema and their end-client required, and within the given timeframe.”
Watch the video