Maximising productivity - the Huisman approach
Staying competitive and adapting quickly in a rapidly changing market is a constant challenge. By building up long-lasting partnerships with our clients and having a deep understanding of their requirements, we can help maximise productivity of equipment throughout its lifecycle with turnkey upgrades and modifications.
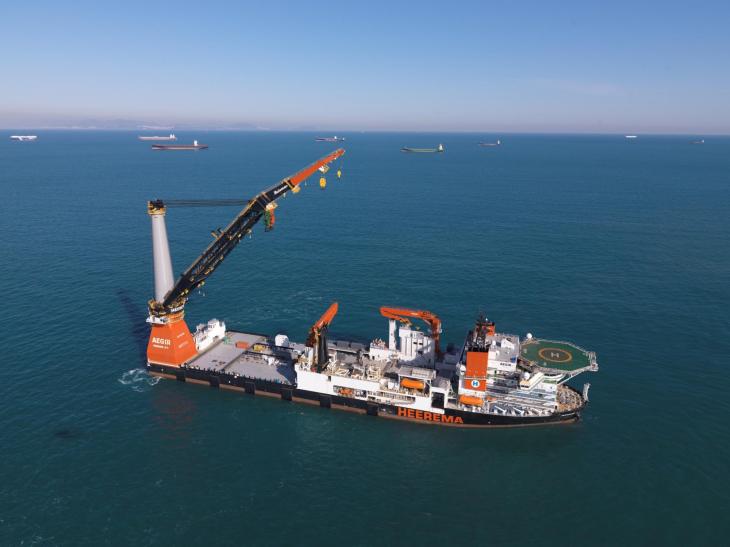
Huisman has the in-house engineering knowledge, experience and production capabilities to make sure equipment is futureproof. We understand the importance of remaining competitive in a constantly changing market. The speed of change, particularly in the offshore wind sector, means that upgrades are a cost-effective solution.
Huisman is continuously developing new technologies and solutions. While our latest technical innovations are often installed on newbuilds initially, in most cases they can be retrofitted to existing equipment, and this can be early or late in the lifetime of the equipment.
Huisman thrives on technical challenges
Koen de Vette, Proposal Lead Services Department, comments: “Huisman is an experienced and innovative service provider in every phase of the equipment’s lifecycle. We have decades of experience as a manufacturer and as a multidisciplinary engineering company.
“Our expert engineers will never say ‘no’ to a technical challenge. They want to partner our clients to make the seemingly ‘impossible’ happen. Our motto is ‘if clients are successful, then we’re successful!”
Given Huisman’s highly qualified professionals, technically a lot is possible, Bas van der Ploeg, Manager Engineering Services, emphasises. “Because of our extensive engineer experience we can look at the project from multiple angles and also involve Class from an early stage of the project. And we always make sure we are in the driver’s seat when considering safety and quality.”
Proactive role to inform clients about future equipment needs
They point out that Huisman is very much taking a proactive role in supporting clients to keep up with industry developments.
“There are a lot of vessels out there with obsolete parts We can give the owners a heads up that in the next few years they have a significant capital expense coming along. We are working closely with clients to inform them what will be obsolete in the coming five years and offer advice about strategic spare parts packages and how to modernise their systems and equipment,” says Jerry Donker, Manager Service Offering, who is responsible for managing technical proposals, modifications and requests for clients.
Huisman global production capacity
For upgrades & modifications, Huisman has its own production facilities in the Netherlands, China, Brazil and the Czech Republic, as well as sales, service and engineering offices worldwide.
The largest production facility in China represents a total yard area of 284,000m2, of which 58,000m2 is covered. The production yard can handle even the biggest projects, and is able to hoist 2,000mt in the shop and 2,600mt @ 30m on the quayside.
But to always work shoulder to shoulder with the client, Huisman also carries out upgrades at shipyards that the client has chosen and considers the most convenient location for them. “We understand that bringing a vessel out of its schedule and berthing alongside a quayside for days of upgrade work is a costly business. We want to make sure our clients’ vessels are on their way again as soon as possible,” says Bas.
How does the upgrade process work?
Typically, a dedicated team of engineers from the Engineering Services’ team, led by Bas, becomes involved during the concept phase and discusses what modifications are possible with the client and outlines the fabrication schedule.
Multiple engineering stages
- A Concept/System Engineering stage – a small Huisman team working closely with the client’s project team to obtain their input. At this stage, an Account Manager is assigned as the contact person and a Proposal Lead also joins and is responsible for the proposal/quotation. The Proposal Lead gets in contact with the engineering department to make sure the client gets a comprehensive quotation as quickly as possible.
- If the upgrade is involving a big overhaul, a Project Manager is also involved and a multidisciplinary project a team is created, and this can be from several Huisman locations worldwide.
- Basic engineering – after this important stage the materials/capital parts are ordered. The main calculations are performed, covering specifications such as plate sizes and all the capital parts.
- Then the Detailed and Manufacturing engineering phases take place. And at every stage, the same Huisman engineers are still involved to optimise continuity and communication with the client.
Client case – Heerema Marine Contractor’s ‘Aegir’ monohull crane vessel
In a good example of how Huisman supports its clients throughout the entire lifetime of their equipment, we have performed two crane upgrades on Heerema’s ‘Aegir’, one of the largest monohull crane vessels in the world.
In 2021, the lifting capacity of the main hoist was successfully increased from 4,000 to 5,000mt, alongside several other modifications. And then during the latest upgrade, the lifting capacity of the second main hoist was increased from 2,000mt to 3,200mt, at a height of 110 m, making the vessel ideal for the installation of large jacket foundations.
The decision to carry out this upgrade was prompted by developments in the offshore wind sector and shifting client requirements. Heerema was looking to gain some additional flexibility from its second main hoist. Higher lifting heights are needed to handle larger and heavier foundations and components.
As Heerema and Huisman have worked closely together for many years, the project soon got underway. The two companies quickly identified the most suitable location for manufacturing the crane section and where the Installation, Commissioning and Testing should take place. Huisman fabricated the new boom section, weighing 160mt, at its own facility in China, which is the Group’s largest production facility, representing a total yard area of 284,000 m2. Heerema then picked the section up in China and shipped it to Singapore for installation.
Really tight planning was in place for the ICT period of just 94 days. All the components had to be in Singapore, as well as a large team of Huisman engineers from Huisman’s various locations worldwide. The timeline and risk management were critical. Given that some items such as large bearings could have a lead-time of 36-40 weeks and the hook casting 40 weeks, it was vital to order crucial parts on time.
Despite the complexity of the upgrade, the technical challenges, tight schedule, and logistics, Huisman could deliver the project to Heerema’s requirements in a very short timeframe and successfully meet the schedule.
With more than 90 years of experience and engineering expertise built up, this large-scale project demonstrates how Huisman is a reliable partner for every phase of the equipment’s lifecycle. Our long-lasting, fruitful partnerships with our clients help us to anticipate their future needs. We support them in adapting their equipment, so they stay ahead of their competitors in a rapidly changing market.
Our turnkey upgrades and modifications ensure optimal productivity, and that equipment is fit-for-purpose today, and into the future.